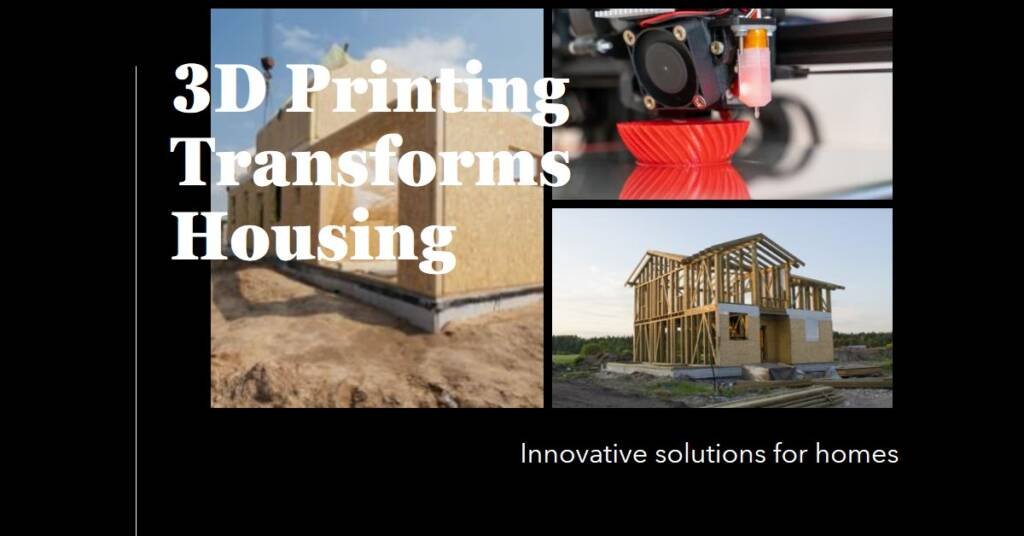
Table of Contents
- Introduction to 3D Printing and Prefabricated Housing
- The Advantages of 3D Printing in Housing
- Innovative Designs Made Possible by 3D Printing
- Case Studies: Successful 3D Printed Housing Projects
- Challenges Facing 3D Printed Housing
- The Future of 3D Printing in Housing
- Environmental Impact of 3D Printed Homes
- Global Perspectives: Adoption of 3D Printing in Different Regions
- Conclusion: Embracing the Revolution in Housing
Introduction to 3D Printing and Prefabricated Housing
3D printing, also known as additive manufacturing, refers to a transformative technology that creates three-dimensional objects through a layer-by-layer construction process. This innovative approach began gaining traction in the 1980s and has since evolved, offering a diverse range of applications across various industries, including healthcare, aerospace, and notably, construction. By utilizing computer-aided design (CAD) software, 3D printing allows for the design and production of complex structures that were previously unachievable using traditional manufacturing techniques.
Prefabricated housing, on the other hand, encompasses a construction method wherein building components are manufactured in a factory setting before being transported to the designated site for assembly. This technique enhances efficiency, reduces waste, and accelerates the construction time while maintaining quality and safety standards. Traditionally, prefabricated homes have evolved from modular designs to more complex prefabricated systems that integrate various construction techniques to create livable spaces quickly and cost-effectively.
The intersection of 3D printing and prefabricated housing represents a significant evolution in the construction industry. The introduction of 3D printing into the prefabrication process heralds a new era of construction that promises greater customization, reduced labor costs, and improved sustainability. By employing 3D printers to manufacture home components, builders can produce tailored housing solutions that meet specific client needs while minimizing material waste and energy consumption. This synergy facilitates a streamlined production pipeline—combining advanced manufacturing practices with the reliability of prefabrication—which effectively addresses the urgent demand for affordable housing in a rapidly urbanizing world.
The Advantages of 3D Printing in Housing
The advent of 3D printing technology has marked a significant turning point in the field of housing construction. One of the primary advantages that 3D printing brings to this sector is substantial cost savings. Traditional construction methods often involve high labor expenses and material costs, which can burden both builders and homeowners. In contrast, 3D printing minimizes labor requirements through automation and can utilize less expensive construction materials, ultimately reducing the overall cost of building a home. Moreover, numerous small-scale projects have demonstrated that utilizing 3D printing can decrease expenses by as much as 30%.
Another notable benefit of 3D printing in housing is the reduction of waste. Conventional construction techniques typically generate significant waste through excess materials and offcuts. Conversely, 3D printing utilizes materials more efficiently, producing precision components that fit together seamlessly, which minimizes leftover materials. This sustainable approach not only aligns with environmentally friendly practices but also contributes to decreased disposal costs and a lower carbon footprint in housing developments.
Enhanced design flexibility is also a critical advantage of 3D printing technology in housing. With traditional construction, architects face limitations regarding design complexity due to material constraints. However, 3D printing allows for the creation of intricate designs that were previously infeasible or prohibitively expensive. This capability enables builders to explore innovative architectural concepts, which can lead to aesthetically pleasing and functional living spaces tailored to the homeowner’s vision.
Furthermore, 3D printing significantly reduces construction timelines. Homes can be printed in a matter of days rather than months, expediting the construction process. This accelerated timeline enables quicker occupancy, which is particularly beneficial in response to urgent housing crises or demand for affordable housing solutions. Customized home designs can also be rapidly adapted to meet specific needs, increasing personal satisfaction and allowing for modifications on-the-go. Real-world projects, such as 3D printed homes in Mexico and the United States, validate the efficiency and effectiveness of this transformative technology in contemporary housing.
Innovative Designs Made Possible by 3D Printing
The advent of 3D printing technology has significantly transformed the landscape of architectural design, particularly in the field of prefabricated housing. This innovative approach allows architects and builders to create structures that were previously deemed impractical or even impossible using traditional construction methods. One of the most striking advantages of 3D printing in construction is its ability to produce complex geometries that challenge conventional design norms. Through additive manufacturing techniques, intricate forms, including organic shapes and multifaceted structures, can be realized with precision and efficiency.
These unique designs are not only visually captivating but also serve functional purposes. For example, the use of 3D printing enables the construction of structures that optimize energy efficiency, enhancing their sustainability. By utilizing materials that reflect natural light or thermoregulate spaces, architects can create aesthetically pleasing homes that contribute to a reduced ecological footprint. Furthermore, environmental considerations are gaining momentum, and 3D printing can facilitate the use of eco-friendly materials, paving the way for greener construction practices.
Additionally, the customization potential offered by 3D printing is unparalleled. Homebuyers can collaborate closely with architects to tailor designs to meet their specific requirements, reflecting personal tastes while maintaining cost-effectiveness. The ability to print unusual shapes or easily alter designs based on site conditions or local housing demands exemplifies how 3D printing offers not just creativity but practicality.
In summary, 3D printing is ushering in a new era of innovative designs in prefabricated housing. By enabling the production of complex geometries and eco-friendly structures, this technology not only pushes the boundaries of architectural possibilities but also champions sustainable living practices, thereby rendering it a vital component of future residential construction.
Case Studies: Successful 3D Printed Housing Projects
The advent of 3D printing technology has enabled innovative approaches to housing, with numerous successful projects emerging globally. One noteworthy case is the ICON project in Austin, Texas, which aims to address the affordable housing crisis faced by many cities. The team at ICON developed a method called Vulcan, which uses a proprietary concrete mixture to 3D print homes in a fraction of the time traditional construction methods require. Each unit is printed in less than 24 hours, providing a practical solution for creating affordable living spaces rapidly. The initial designs focus on providing safe, resilient, and environmentally friendly structures for individuals and families in need, illustrating the immense potential of 3D printing in social housing initiatives.
Another compelling example comes from Mexico, where the non-profit organization New Story partnered with ICON to construct a sustainable 3D printed community. Located in the state of Tabasco, the project consists of a series of 3D printed homes, each designed with modern amenities, while maintaining a focus on affordability and durability. This venture not only demonstrates the viability of 3D printing technology in building homes but has also enabled community engagement, as local families are part of the design process. By empowering residents to participate, the project fosters pride in ownership and showcases how innovative construction techniques can directly benefit communities.
In Europe, a groundbreaking initiative took place in the Netherlands, where a company named Kamp C launched a project that incorporated both 3D printing and sustainable building practices. Their aim was to create a fully functional house built from renewable resources, demonstrating how 3D printing can contribute to ecological sustainability. This project set a benchmark for future developments, emphasizing the need for sustainable materials and energy efficiency in construction. The positive societal impacts of these projects extend beyond mere housing solutions, often facilitating economic growth and community development in areas where they are implemented.
Challenges Facing 3D Printed Housing
While 3D printing technology offers significant advantages for prefabricated housing, various challenges hinder its widespread adoption in the construction industry. One primary concern revolves around regulatory and building code compliance. Authorities must adapt existing regulations to accommodate this innovative construction method, which often contradicts traditional building practices. As local governments grapple with these adaptations, the lack of clear guidelines can delay projects and impede the growth of the 3D printed housing market.
Another obstacle is public perception. Many consumers may be hesitant to embrace 3D printed homes due to concerns about their durability and safety. Misinformation surrounding the technology can exacerbate this skepticism, leading to a perception that these homes are substandard or unsuitable for long-term living. To address this issue, industry stakeholders need to engage in robust public outreach and education campaigns that highlight the benefits and reliability of 3D printed structures.
Material reliability poses additional challenges for the construction of 3D printed homes. While various materials have been developed for use in 3D printing, not all offer the same level of strength, insulation, and durability as conventional building materials. Ongoing research is essential to enhance the quality of these materials and ensure their long-term performance. Further, technological limitations such as scaling issues for larger projects and the need for specialized equipment for various printing techniques can hinder the efficiency of 3D printed housing.
Despite these challenges, potential solutions are being explored. Collaborations between researchers, industry professionals, and regulatory bodies are increasingly crucial. By developing standardized codes, enhancing public understanding, and advancing material science, the construction community can navigate these hurdles and potentially revolutionize the prefabricated housing industry through 3D printing.
The Future of 3D Printing in Housing
The realm of 3D printing technology in prefabricated housing is poised for significant innovation and expansion. As advancements in materials science continue to emerge, new composite materials are being developed that enhance the durability, insulation, and sustainability of 3D-printed structures. For instance, the integration of recycled plastics and agricultural waste into printing materials not only reduces waste but also supports environmentally responsible building practices. These materials promise to lessen the carbon footprint associated with traditional construction methods, ultimately contributing to more sustainable housing solutions.
Moreover, the processes involved in 3D printing are evolving to become faster and more cost-effective. Techniques such as robotic 3D printing and the use of large-scale printers allow for rapid construction of homes, thereby reducing labor costs and construction time. This efficiency not only makes housing more accessible but also helps address urgent housing shortages in urban areas. In the context of prefab housing, this innovative manufacturing process can lead to the production of customized designs that meet the specific needs of diverse communities, promoting inclusivity in housing development.
Furthermore, with the increasing integration of smart home technology, 3D-printed houses are likely to evolve into intelligent living spaces. By incorporating embedded sensors and Internet of Things (IoT) devices, these homes can offer enhanced energy efficiency, security, and convenience. Smart systems could manage utilities more effectively, monitor occupancy levels, and facilitate maintenance, creating a living environment that is not only sustainable but also adaptable to modern lifestyles.
In essence, the future of 3D printing in housing heralds a paradigm shift, impacting urban planning and reshaping living environments. The potential for this technology to streamline construction, promote sustainability, and enhance the quality of life can lead us towards a more responsive and resilient urban landscape.
Environmental Impact of 3D Printed Homes
The emergence of 3D printing technology has led to profound implications for the construction industry, particularly within the realm of prefabricated housing. One significant aspect of this transformation is its environmental impact. Traditional construction practices often generate substantial waste, whereas 3D printing minimizes excess material use. This technology allows for precise measurements and eliminates the need for surplus components, consequently leading to an overall reduction in waste generation.
Moreover, 3D printed homes typically exhibit improved energy efficiency, as their design can easily incorporate innovative insulation materials and techniques. By utilizing advanced building methods, these homes can achieve superior thermal performance, reducing the energy required for heating and cooling. As a result, 3D printed residences contribute to lower energy consumption over their lifetime, aligning with global efforts to mitigate climate change.
The pursuit of sustainable materials is another critical facet of the eco-friendliness of 3D printed homes. Many manufacturers are exploring the use of biodegradable and recyclable materials such as bioplastics and natural composites, significantly lowering the environmental footprint of construction. By choosing materials that minimize carbon emissions and offer longevity, the 3D printing industry is fostering a shift toward sustainable building practices.
Finally, the potential of 3D printing technology to support eco-friendly construction practices cannot be overstated. The capacity to fabricate complex structures onsite reduces the necessity for extensive transportation logistics, which in turn decreases emissions associated with material delivery. Furthermore, 3D printing can promote community engagement in sustainable building initiatives by making the construction process more accessible, encouraging local participation in crafting eco-friendly living spaces.
Global Perspectives: Adoption of 3D Printing in Different Regions
The adoption of 3D printing technology in the construction of prefabricated housing varies significantly across different regions, influenced by technological advancements, regulatory frameworks, and economic conditions. In North America, for instance, companies have begun to recognize the potential of 3D-printed homes as a solution to affordable housing crises. The United States has seen innovative projects that utilize advanced materials and techniques, resulting in reduced construction times and costs. These developments have been encouraged by a relatively flexible regulatory environment, allowing for rapid integration of 3D printing technology in residential construction.
In contrast, European countries exhibit a more cautious approach. Nations such as the Netherlands and Germany have been at the forefront of implementing 3D printing in housing, driven by strong governmental support and funding for research initiatives. These countries emphasize sustainability and energy efficiency, prompting the adoption of 3D printing methods that align with their environmental goals. Various pilot projects across Europe illustrate the capability of 3D printing to deliver eco-friendly housing solutions while addressing local housing shortages.
Meanwhile, in parts of Asia, countries like China are rapidly advancing their use of 3D printing technology in construction. The Chinese government actively promotes innovations within the construction sector, providing funding and resources to facilitate large-scale 3D printing projects. This aligns with broader efforts to address urbanization challenges and promote efficient housing solutions for growing populations. However, the regulatory framework surrounding 3D printing in China can sometimes pose challenges, with varying local regulations affecting the implementation speed of these projects.
Overall, the global landscape of 3D-printed housing reveals a complex interplay of local economic conditions and regional priorities. While some countries fully embrace this transformative technology, others remain cautious, highlighting the diverse perspectives on the future of prefabricated housing worldwide.
Conclusion: Embracing the Revolution in Housing
In an era where rapid advancements in technology significantly influence various sectors, the adoption of 3D printing in prefabricated housing stands out as a transformative force. This revolutionary approach offers a compelling solution to pressing challenges within the housing market, particularly in relation to shortages, affordability, and sustainability. As discussed throughout this blog post, 3D printing technology empowers the construction industry to develop homes more efficiently, reduce material waste, and ultimately lower associated costs.
One of the most critical points to highlight is the growing prevalence of housing shortages in numerous urban locations worldwide. Conventional building methods often fall short in meeting the soaring demand for immediate and accessible housing options. By embracing 3D printing, cities can expedite construction timelines, resulting in homes that are ready for occupancy within weeks rather than months or years. This capability is crucial in addressing the urgent needs of communities struggling with inadequate housing.
Furthermore, 3D printing fosters innovation in design and construction techniques, enabling architects and builders to craft highly customized homes that cater to the unique requirements of various demographics. The ability to produce complex structures with minimal labor involved not only optimizes resources but also streamlines the building process. This advancement contributes to an overall reduction in project costs, paving the way for more affordable housing solutions, particularly for first-time homeowners and low-income families.
Lastly, the integration of 3D printing in housing construction aligns with sustainable practices by utilizing eco-friendly materials and reducing carbon footprints. As prefabricated housing continues to evolve, investing in this cutting-edge technology will undoubtedly play a pivotal role in shaping the future of urban living. Embracing the revolution in housing through 3D printing is essential for creating a more accessible, sustainable, and efficient housing landscape for generations to come.