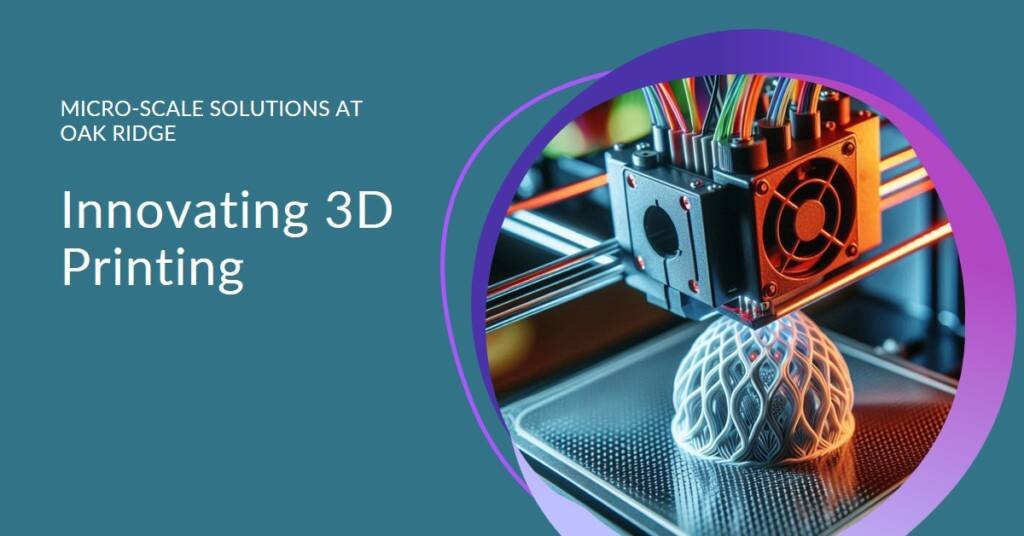
Table of Contents
- Introduction to Micro-Scale 3D Printing
- Overview of Oak Ridge National Laboratory (ORNL)
- The Innovation Process Behind Micro-Scale 3D Printing at ORNL
- Key Technological Advancements in Micro-Scale 3D Printing
- Applications of Micro-Scale 3D Printing
- Benefits of Using Micro-Scale 3D Printing in Manufacturing
- Future Prospects of Micro-Scale 3D Printing
- Challenges and Limitations of Micro-Scale 3D Printing
- Conclusion: The Impact of ORNL’s Innovation on the Future of Manufacturing
Introduction to Micro-Scale 3D Printing
Micro-scale 3D printing represents a transformative approach within the manufacturing industry, allowing for the fabrication of extremely small parts with intricate geometries. This innovative technology builds on the foundational principles of 3D printing, where digital models are converted into physical objects through an additive process. The evolution of 3D printing has progressed from prototyping simple components to creating highly complex structures that cater to specific industry needs, and micro-scale techniques play a pivotal role in this advancement.
The significance of micro-scale 3D printing lies in its ability to produce components that traditional manufacturing cannot achieve. Such components often require high precision and fine detailing, which are essential in sectors like healthcare, electronics, and aerospace. For instance, micro-scale 3D printing has enabled advancements in creating micro-level scaffolds for tissue engineering, where the precision of manufacturing is critical for cell growth and functionality. This level of detail opens up possibilities for innovation that is both cost-effective and time-efficient compared to conventional manufacturing methods.
Moreover, these advanced techniques utilize various materials, including polymers, metals, and ceramics, allowing for diverse applications that extend beyond simple designs. With micro-scale 3D printing, the intricate designs can be tailored to meet the specific requirements of the application, making it invaluable for high-performance needs. As a result, industries benefit not only from enhanced performance but also from the reduction of waste, as additive manufacturing techniques utilize only the necessary material to produce the desired product.
In essence, micro-scale 3D printing marks a significant turning point in the way we approach design and manufacturing. By leveraging this innovation, industries are poised to embrace more complex designs, thus streamlining production and yielding products that were previously unimaginable.
Overview of Oak Ridge National Laboratory (ORNL)
Oak Ridge National Laboratory (ORNL) is the largest science and energy national laboratory in the U.S. Department of Energy, located in Oak Ridge, Tennessee. Established in 1943, the laboratory has contributed significantly to the fields of materials science, energy production, and environmental sustainability. One of ORNL’s primary missions is to conduct transformative research that addresses national and global challenges through innovation and scientific excellence.
Over the decades, ORNL has made notable advancements in numerous scientific domains, particularly in materials science and engineering. With the advent of sophisticated computational tools and experimental techniques, ORNL has been at the forefront of developing new materials that contribute to various industries. The laboratory champions the integration of research with practical applications, positioning itself as a key player in pushing technological boundaries.
ORNL is also recognized for its pioneering work in 3D printing innovation. The laboratory is dedicated to advancing additive manufacturing processes and has developed several cutting-edge technologies in this area. By leveraging its extensive expertise in materials science, ORNL has effectively positioned itself as a leader in 3D printing technologies, contributing to both fundamental research and the development of new manufacturing methods. These efforts not only enhance the efficiency of traditional production techniques but also open doors for creating complex geometries and customized products that were previously unattainable.
Furthermore, ORNL’s collaborative approach brings together various stakeholders, including academic institutions, industry partners, and governmental organizations, to foster a thriving ecosystem of innovation. Through initiatives and programs aimed at sharing knowledge and advancements in 3D printing, ORNL continues to play a pivotal role in enhancing the capabilities of manufacturing and engineering sectors.
The Innovation Process Behind Micro-Scale 3D Printing at ORNL
The development of micro-scale 3D printing technology at Oak Ridge National Laboratory (ORNL) represents a significant advance in manufacturing capabilities, driven by a methodical innovation process. This journey begins with rigorous research methodologies aimed at understanding the fundamental principles of micro-fabrication. Scientists at ORNL deploy a multidisciplinary approach, integrating insights from materials science, engineering, and computer-aided design, to explore potentially groundbreaking applications of micro-scale printing.
A crucial aspect of this innovation process is the iterative experimentation that revolves around refining 3D printing techniques. Researchers utilize advanced software models to simulate printing processes and predict outcomes, allowing them to identify optimal parameters before physical trials. This analytical phase helps to mitigate the challenges often encountered in micro-fabrication, such as resolution limits and material compatibility. Continuous feedback loops inform the development process, enabling the team to adapt and enhance their methods swiftly.
Equally important to the innovation process is the collaborative spirit that permeates ORNL’s research environment. A diverse team of scientists and engineers works in unison, often crossing disciplinary boundaries to solve complex problems. This collaborative effort is essential in overcoming the logistical and technical challenges inherent in micro-scale 3D printing. For instance, the investigation into new materials, such as photopolymers and metal alloys, necessitates input from various expertise areas, resulting in significant breakthroughs in the capabilities of micro-printing technology.
Despite the hurdles faced, such as scaling experimental findings to practical applications, the ongoing dedication to research and development at ORNL fosters an environment ripe for innovation. The focus on micro-scale 3D printing not only enhances manufacturing processes but also opens new avenues for applications in industries ranging from healthcare to aerospace. Ultimately, the synergy between innovative methodologies and collaborative efforts is central to the successes achieved at ORNL in advancing the field of micro-scale 3D printing innovation.
Key Technological Advancements in Micro-Scale 3D Printing
The landscape of manufacturing has transformed significantly, thanks in large part to key technological advancements in micro-scale 3D printing, prominently contributed by the Oak Ridge National Laboratory (ORNL). Among the principal breakthroughs is the development of new materials that facilitate unprecedented levels of detail and functional performance. These materials offer enhanced mechanical properties, thermal resistances, and the capability to integrate multiple functionalities into a single print. By utilizing novel polymer composites, ORNL has pushed the boundaries of what’s achievable in micro-scale applications.
Equally significant are improvements in the precision of the printing processes themselves. ORNL has refined its techniques, enabling the creation of intricate geometries that were previously deemed impractical in the micro-scale 3D printing realm. Employing advanced laser sintering and digital light processing, the lab enhances resolution levels and reduces printing times, resulting in a more efficient manufacturing pipeline. This not only accelerates production rates but also allows for a broader scope of applications, catering to industries that demand high precision such as aerospace and medical devices.
In addition to materials and processes, innovative design methodologies have emerged, emphasizing the integration of computer-aided design (CAD) with additive manufacturing. This synergy empowers engineers to design components that optimize weight and material usage without compromising structural integrity. The iterative design capabilities inherent in micro-scale 3D printing allow for rapid prototyping and testing, enabling manufacturers to innovate swiftly in response to evolving market demands.
Overall, these technological advancements mark significant milestones in the field of micro-scale 3D printing. By enhancing the available materials, refining printing processes, and developing sophisticated design methodologies, ORNL is leading the way toward a future where micro-scale 3D printing innovation will play a pivotal role in revolutionizing the manufacturing landscape.
Applications of Micro-Scale 3D Printing
Micro-scale 3D printing innovation, particularly as developed at the Oak Ridge National Laboratory (ORNL), is making significant strides across various sectors including aerospace, medicine, electronics, and automotive manufacturing. These advancements are not only enhancing product functionality but are also transforming traditional manufacturing processes into more efficient and precise methods of production.
In the aerospace industry, micro-scale 3D printing technology allows for the creation of lightweight components that meet the rigorous standards of aviation engineering. For example, the ability to fabricate intricate geometries and complex designs enables aerospace engineers to optimize fuel efficiency and reduce the overall weight of aircraft. This innovation paves the way for new designs that were previously impossible using conventional manufacturing techniques, thus enhancing performance and safety.
In the realm of medicine, micro-scale 3D printing has revolutionized the production of personalized medical devices. Custom implants and prosthetics can be developed with precision that aligns with the unique anatomy of individual patients, increasing comfort and functionality. Moreover, this technology has facilitated rapid prototyping of medical equipment, allowing for faster product development cycles and enhanced adaptability in surgical procedures.
The electronics sector is also benefiting from micro-scale 3D printing innovation. The ability to print miniaturized components, such as sensors and circuit boards, has opened new avenues for the development of compact and efficient electronic devices. This innovation directly contributes to the miniaturization trend observed in consumer electronics, increasing their performance while decreasing size.
Lastly, in the automotive industry, the integration of micro-scale 3D printing technologies enables manufacturers to produce complex parts on-demand, significantly reducing waste and lead times. By allowing for the customized production of specialized components while maintaining high levels of accuracy, this innovation is transforming how vehicles are designed and produced, ultimately enhancing overall efficiency.
Benefits of Using Micro-Scale 3D Printing in Manufacturing
The advancement of micro-scale 3D printing innovation stands to significantly alter the landscape of manufacturing. One of the primary benefits associated with this technology is its cost-effectiveness. Traditional manufacturing methods often require substantial investments in tooling and production setups. In contrast, micro-scale 3D printing requires fewer resources and can efficiently produce intricate designs without the need for extensive tooling. This reduction in overhead can lead to decreased production costs, making it an attractive alternative for manufacturers.
In addition to cost savings, micro-scale 3D printing enhances time efficiency. The iterative design process is dramatically accelerated, as prototypes can be developed and tested rapidly. Manufacturers can expect quicker turnaround times for product development, allowing them to respond swiftly to market demands and trends. Moreover, the technology’s ability to produce complex geometries in a single step reduces the need for multiple manufacturing processes, further saving time in production workflows.
Customization capabilities also emerge as a notable advantage of micro-scale 3D printing. Manufacturers can create bespoke products tailored to specific customer requirements without compromising on quality or incurring exorbitant costs. This level of customization allows for greater personalization in product offerings, which can enhance customer satisfaction and foster brand loyalty.
Sustainable practices are another benefit intertwined with the use of 3D printing technologies. The micro-scale approach produces minimal waste compared to traditional manufacturing processes, as materials are deposited layer by layer rather than being cut away from a larger block. This reduction in waste not only contributes positively to environmental considerations but also maximizes material utilization, making the entire manufacturing process more resource-efficient.
Overall, the integration of micro-scale 3D printing innovation into manufacturing processes delivers several compelling benefits, including cost-effectiveness, time efficiency, customization capabilities, and sustainable practices, paving the way for a modernized approach to production.
Future Prospects of Micro-Scale 3D Printing
The realm of micro-scale 3D printing innovation holds significant promise for the future of manufacturing. As the technology evolves, key advancements are anticipated that could further transform various industries. One of the most compelling trends is the ongoing miniaturization of 3D printing processes. With the capability to create intricate and highly detailed components at microscopic levels, manufacturers will be able to produce parts that were previously impossible to fabricate using traditional techniques. This could lead to breakthroughs in fields such as electronics, medical device manufacturing, and aerospace engineering.
Moreover, the integration of advanced materials into 3D printing processes is expected to enhance the performance and applications of micro-scale products. Innovations in polymer science and metal alloys could result in materials that are not only lighter and stronger but also offer unique properties such as self-healing capabilities or biocompatibility. The ability to develop custom materials tailored to specific applications will further elevate the role of micro-scale 3D printing in modern manufacturing practices.
Another area of interest is the automation and digitalization of the 3D printing workflow. Smart manufacturing practices will play a crucial role in ensuring that micro-scale 3D printing can be adopted at scale. The implementation of machine learning algorithms and artificial intelligence can optimize design processes, streamline production, and improve quality control. These technologies will enable organizations like Oak Ridge National Laboratory (ORNL) to maintain their leadership position in innovation within the field.
In conclusion, the prospects for micro-scale 3D printing are promising, driven by emerging technologies and materials that will redefine manufacturing capabilities. Organizations committed to advancing this technology, such as ORNL, are poised to lead the charge, fostering innovation and exploring new applications that will change the landscape of manufacturing in the coming years.
Challenges and Limitations of Micro-Scale 3D Printing
Micro-scale 3D printing innovation offers exciting possibilities for manufacturing, yet it is not without its challenges and limitations. One of the primary technical obstacles in this emerging field is the restriction of materials that can feasibly be used. Traditional 3D printing materials, such as certain plastics and metals, may not perform well at micro scales. Developing materials specifically designed for micro-scale applications is essential for ensuring the mechanical strength, thermal stability, and overall performance of the printed components.
Another considerable challenge is scalability. While advancements in micro-scale 3D printing have demonstrated potential for producing intricate designs, transitioning these technologies from laboratory settings to large-scale manufacturing remains complex. The current methods, often tailored to small batch sizes, must be optimized to handle mass production without compromising quality or increasing costs. This often requires innovative approaches to streamline the production process while maintaining high fidelity in the printed structures.
Moreover, the precision required for micro-scale 3D printing pushes the limits of existing technology. Issues such as dimensional accuracy and resolution become more pronounced, necessitating significant enhancements in printer capabilities and techniques. For instance, resolving issues with layer adhesion and achieving seamless integration of features at reduced sizes demands continuous research and development to overcome these barriers.
Finally, the regulatory environment surrounding the adoption of micro-scale 3D printing technologies poses its own set of challenges. Ensuring compliance with industry standards and gaining necessary approvals can slow the pace of development and innovation. Addressing these limitations is crucial for the broader application of micro-scale 3D printing, and ongoing efforts in research and development will be imperative to unlock its full potential in manufacturing.
Conclusion: The Impact of ORNL’s Innovation on the Future of Manufacturing
As explored in this blog post, the advancements brought forth by the Oak Ridge National Laboratory (ORNL) in micro-scale 3D printing innovation stand to revolutionize conventional manufacturing processes. By enabling unprecedented precision and efficiency, this technology signifies a paradigm shift in how industries conceptualize and produce goods. The integration of micro-scale 3D printing into various sectors not only fosters enhanced product performance but also promotes sustainability by minimizing waste through additive manufacturing techniques.
The implications of ORNL’s research extend beyond mere manufacturing enhancements. This innovation provides a pathway for creating complex geometries and customized products that were previously unattainable with traditional methods. Industries such as aerospace, automotive, and medical are poised to benefit enormously from the ability to rapidly prototype and manufacture components on-demand, thus reducing lead times and costs significantly. This evolution in manufacturing could lead to a more agile supply chain, responding to consumer demands more dynamically than ever before.
Moreover, the enduring collaboration between public institutions like ORNL and private manufacturers amplifies the impact of these innovations. Joint research efforts and knowledge sharing enhance technical expertise across sectors, encouraging an environment ripe for further advancements in 3D printing technology. All these factors combine to position ORNL’s contributions as a catalyst for future developments in manufacturing, suggesting that the journey towards a more efficient, sustainable, and customizable production landscape is only just beginning.
In summary, the micro-scale 3D printing innovations emerging from Oak Ridge National Laboratory hold the potential to redefine manufacturing benchmarks and practices. By embracing these advancements, the manufacturing sector can look forward to a transformative future, where innovation and adaptability will be key drivers of success.